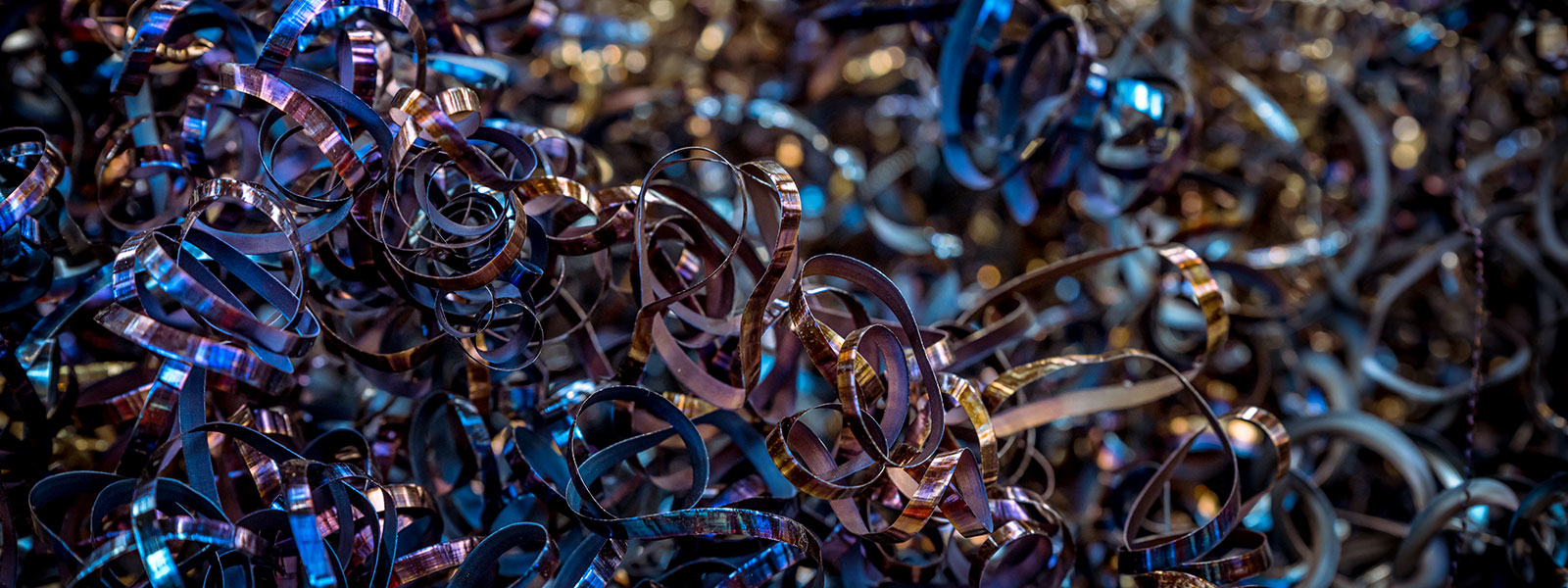
From trash to treasure: Green metals from recycling
The global drive towards a low-carbon circular economy and increased focus on ESG are creating many new opportunities for metal recycling projects. But is scrap the answer to the growing demand for green metals?
13 min read
Subscribe
Stay current on your favorite topics
Improving ESG credentials is an area of increasing focus for all industries. When leading decision-makers in the mining & metals sector were asked as part of the White & Case 2022 Mining & Metals Survey what significant structural changes the mining & metals industry expected to see as a result of the increased focus on ESG, the second most common response was a greater emphasis on green metal, including recycling. Although early-stage, this has begun to play out, with industry players seeking to capitalize on the opportunity.
The push for green metals, and the role of increased recycling
The refining and processing of metals is one of the most significant sources of greenhouse gas emissions globally. With their particularly energy-intensive processes, the aluminum and steel industries are alone estimated to contribute 2 percent and 7 percent respectively of all global CO2 emissions.
As the ESG spotlight shifts onto the mining & metals sector, a space is being created for the production of "green metals," with players in the mining & metals sector working to reduce the direct emissions from their metal production facilities, and consumers increasingly focused on the ESG credentials and indirect emissions of the metals consumed in their supply chain. As part of this trend, there is increased interest in recycling as a source of green metals.
The ideas around the circular economy, where all aspects of the economy are re-purposed and/or re-used, align well with recycling. Relatively high commodity prices also make the often resource-intensive process of sorting and processing scrap more economically viable. Smelting scrap metal for recycling also requires significantly less energy than the initial process of refining raw minerals into metals, meaning lower emissions. Finally, the shake-up of global supply chains by COVID-19 and geopolitical conflict has also shone a light on the downsides of global supply chain interdependencies, leading countries to look inward for sources of commodities, including the potential uses for scrap.
But are recycling projects the answer to the expected rising demand for green metals? And if these projects do get the "green light" from investors, where will the required scrap come from, and how are these new projects likely to be developed, constructed and financed?
20%
The proportion of global metal output produced from metal scrap is around 20 percent for most widely recycled metals
Scrap as a commodity
Recent estimates indicate that the proportion of global metal output produced using the secondary process (i.e., production from metal scrap) is approximately 20 percent for most widely recycled metals, and this proportion is higher in the steel and aluminum sectors in jurisdictions such as the US and the EU.
Historically, the recycling of metals, such as copper, steel and aluminum, have had higher rates of recycling, because more simple or bulk products can easily be collected, allowing for existing materials to be repurposed or recycled. However, where there are challenges with collecting waste materials, or the separation of the valuable metal is physically difficult or involves a more energy-intensive process, then the economics may not support the case for recycling, thereby resulting in lower rates of recycling for those materials.
Nonetheless, global demand for scrap metal is expected to remain strong over the coming years, owing to increasing demand for metals across a range of industries, such as automotive and construction, as well as ESG considerations that favor the use of recycled materials to reduce carbon emissions. For instance, the European aluminum industry in its Circular Aluminum Action Plan has established a target to satisfy 50 percent of EU demand for aluminum using recycled materials by 2030, compared to the current level of 36 percent.
Given the strong demand for scrap metal and its importance for metals production, several countries have sought to reserve their domestic scrap supplies for their own metals processing industries, including by taxing or prohibiting the exportation of scrap metal. Export restrictions on scrap metal have become more prevalent in recent years, particularly among developing countries, and estimates indicate that approximately 40 percent of globally traded copper waste and scrap (and 30 percent of aluminum and 20 percent of iron and steel waste and scrap) is subject to some form of export restriction. Similar export restrictions, which increase the domestic supply of a raw material, thereby reducing its cost, have been found by the trade authorities in some countries (in particular, the US) to confer unfair benefits to downstream users of the raw material and resulted in the imposition of countervailing duties on imports of the downstream products. A number of jurisdictions with significant metals industries have largely refrained from imposing taxes or prohibitions on scrap metal exports.
Whereas export restrictions on scrap metal are relatively common, few countries impose significant import restrictions on scrap metals. Apart from China, few countries have imposed import prohibitions or quotas on scrap metal, and applied most-favored nation (MFN) tariff rates on scrap metal are relatively low (averaging 3.1 percent for aluminum scrap, 3.1 percent for iron and steel scrap, and 3.3 percent for copper scrap). Scrap metals have rarely been the target of trade remedy measures (i.e., antidumping, countervailing duty and safeguard measures), and are exempt from tariffs the US has imposed on steel and aluminum imports on national security grounds pursuant to Section 232 of the Trade Expansion Act.
40%
Approximately 40 percent of globally traded copper waste and scrap is subject to some form of export restriction
Carbon footprint of recycling metals
Though the processing of smelting metal from scrap uses significantly less energy than the initial process of creating metals from raw minerals, the process of recycling metals still requires significant amounts of energy.
Depending on the metal, the traditional source of energy for metal recycling has either been coal or natural gas, with energy-intensive furnaces heated by the burning of one of these two sources of energy. While this allows scrap to be re-used and avoids waste going to landfill, it creates environmental issues regarding emissions from the recycling process.
Electrification of the smelting process and/or the substitution of gas for hydrogen have been presented as ways for the recycling industry to move away from its current reliance on gas and coal-fired energy. While smelting using electricity or hydrogen has the attraction of not emitting at source (i.e., Scope 1 emissions), there is still the question of how the electricity and hydrogen have been sourced (i.e., Scope 2 emissions).
While the trend toward electrification is growing, and sources of green energy are increasing, the majority of power available on the grid in most countries continues to be sourced from fossil fuels. Green hydrogen is also not yet widely available. As illustrated in the graphic above, to developers looking to source the energy required for recycling projects from green sources.
Though not yet widely available, projects being designed today may wish to design for the inclusion or optionality for the use of hydrogen, on the expectation that green hydrogen will become commercially available in the near term.
As consumers of metals products scrutinize the provenance of the metals in their products, it remains to be seen whether the market will distinguish between the ESG credentials of the scrap actually used in the recycling process. With the market currently placing a limited price premium on green metals (as certified by current guidelines), it remains to be seen whether the market will recognize, and be prepared to pay an additional premium for, recycled metals that have had a completely green life cycle. Even if consumers are willing to pay such a premium, as minerals/metals are mixed during the various stages of the mining, refining and recycling process, tracing and verifying a clear provenance of recycled metals will be impractical and difficult.
Metal recycling sector will continue to be a growth area as it comes to play a larger role in supplying the world’s metal needs in a green and sustainable way
Scrap sorting and preparation
Even if metals are recycled, this does not guarantee they had impeccable ESG credentials. While the concept of recycling has long been synonymous with strong environmental credentials, breaking down products and recovering scrap metal can be labor-intensive, which has traditionally been a driver for waste from industrialized countries being exported to less industrialized countries for sorting and processing. Scrap originating in less industrialized countries also presents its own issues, with scrap metals often retrieved from rubbish dumps by hand, and in some cases by child labor. The process of sorting scrap is also potentially dangerous and environmentally harmful, with hazardous substances leaching into the earth if the process is not properly managed and regulated.
EU regulations also apply to companies importing scrap metals into the EU, with regulations currently in place requiring supply chain audits on importers of tin, tantalum and tungsten, their ores, and gold originating from conflict-affected and high-risk areas, with the aim of curtailing opportunities for armed groups and security forces to trade in such metals. Similar legislation in the US also requires certain companies in their SEC filings to disclose their use of conflict minerals (including conflict metals from scrap). A proposal for broader supply chain audit obligations, aimed at banning products with forced or child labor from the EU market, is also currently under consideration in Brussels.
7%
The steel industry alone accounts for seven percent of all global CO2
Challenges and barriers for the development and financing of new recycling projects for green metals
Developing, constructing and financing new recycling projects for green metals presents a potentially huge opportunity, however a number of challenges and barriers will need to be overcome to see these projects realized.
Design of products in the scrap mix: An increase in recycling rates will require more products that are designed so that the metals in them can be extracted easily and efficiently. Lithium-ion batteries, solar panels and wind turbines, which are all crucial to the energy transition, require many different metals, and have a limited design life. Such products should be designed and manufactured today so that at the end of their life, they can be dismantled and recycled efficiently, with limited labor, energy and loss of component metals. The EU is among the first movers in taking steps to regulate the end-of-life requirement for batteries, and we expect to see other jurisdictions follow.
Limited market indices for green metals: Lack of market indices for certified premium green metals to trade offtake at a premium is a barrier, though the LME requirements for metals are evolving to consider more the provenance of metals, rather than focusing only on factors such as shape, size, weight and metallurgical details.
Reliability of scrap feedstock: A key constraint to further recycling projects is the availability of a regular and reliable supply of feedstock. Recycling projects rely on a network that can consistently provide scrap feedstock. Without a reliable source, such as an exclusive arrangement with a steel mill for steel offcuts, or an arrangement with a municipality with a strong and reliable aluminum can collection record, it can be risky for recycling plant operators to rely solely on procuring feedstock from scrap traders. For projects reliant on importing scrap feedstock from another jurisdiction, export control issues and the other trade issues identified in this article are also significant challenges to the reliability of feedstock.
Technology: While electric arc furnaces are in general proven technology, the move towards electrifying the smelting and recycling process at scale has not been piloted in relation to all metals and all process routes. Investors and lenders will need to be comfortable with the technology before developing the projects at scale, and smaller pathfinder projects may need to be developed between investors and technology providers before traditional lenders are prepared to extend financing.
Reliability of hydrogen feedstock: Projects reliant on hydrogen also currently face a shortage of hydrogen feedstock, particularly green hydrogen.
2030
The EU is considering a mandatory declaration of recycled content for most types of batteries in the short term, with mandatory targets for recycled content for lithium, cobalt, nickel and lead in 2030
Government support for recycling projects
Given the significant number of challenges associated with recycling projects, governments will play a key role in putting in place policies and legislation to promote the viability of recycling projects as part of a transition to a circular economy. Government initiatives may come in the form of providing economic incentives, mandating minimum recovery standards, or providing financial support for recycling projects.
In the European Union, the European Commission has adopted the Circular Economy Action Plan as part of the European Green Deal, which is aimed at facilitating the EU's transition into a circular economy.
An EU proposal regulating batteries and battery waste has on 10 March 2022 passed the first reading stage in the EU Parliament, and has now been referred back to the competent committee for the trilogue discussions between the EU Council, the Parliament and the Commission. The proposal is considering introducing a mandatory declaration of recycled content for most types of batteries in the short term, to be followed by mandatory targets for recycled content for lithium, cobalt, nickel and lead in 2030, with mandatory targets to be increased in 2035.
Aside from regulatory mandates in the EU, a number of funding initiatives include the European Structural and Investment Funds, Horizon 2020 and the LIFE program, where businesses can access funding for circular economy projects.
Other initiatives in the European Union include the establishment of the European Raw Materials Alliance, which assists in the financing and execution of projects that are consistent with the objectives of the alliance. Those objectives include reducing dependence on primary materials through the reuse of existing materials. The European Battery Alliance was also established by the EU to support the development of the battery industry in Europe—one of the priority actions includes securing access to secondary raw materials through the recycling of batteries.
Opportunities for ECA financing
Equipment costs form the largest portion of the capital expenditure required to construct any new metals recycling project. Though individual expertise varies across the different metals, European and American equipment manufacturers continue to lead the market in supplying high-quality equipment to the metals sector.
Procuring equipment from a country with a major export credit agency (ECA) can be a gateway to obtaining ECA financing in relation to part or all of new metal recycling projects, particularly as recycling projects are likely to be viewed by ECAs as having stronger ESG credentials than traditional metals plants.
Green financing
Since the issuance of the first green bond by the European Investment Bank in 2007, the market has seen a proliferation of green bonds and green loans to promote the financing of environmentally sustainable projects. For metals recycling projects, these are eligible as "Green Projects" under both the Green Bond Principles and the Green Loan Principles, as they are considered to be projects that promote a transition to a circular economy. These projects represent a nascent but growing market.
Finding a holistic solution
Despite the narrative of moving toward a circular economy, increasing industrialization and rising standards of living mean that it is not expected that there will be sufficient scrap feedstock alone to satisfy all of the global demand for metals. Technical limitations also mean that there will be a continuing demand for virgin minerals to create certain niche metals. Though mineral mining will continue, the metal recycling sector is still likely to be a growth area, as it comes to play a larger role in supplying the world's metal needs in a green and sustainable way.
Download the full report: From trash to treasure: Green metals from recycling (PDF)
White & Case means the international legal practice comprising White & Case LLP, a New York State registered limited liability partnership, White & Case LLP, a limited liability partnership incorporated under English law and all other affiliated partnerships, companies and entities.
This article is prepared for the general information of interested persons. It is not, and does not attempt to be, comprehensive in nature. Due to the general nature of its content, it should not be regarded as legal advice.
© 2022 White & Case LLP